Lighting Requirements and Considerations for Grain Stores
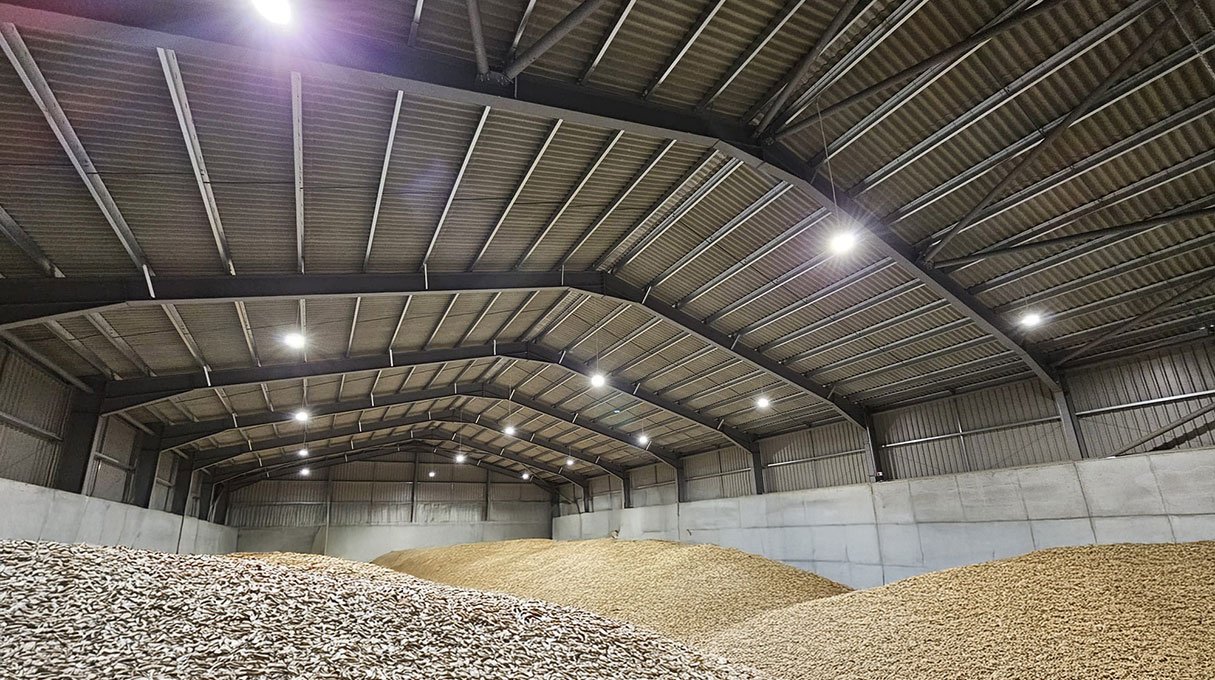
Grain storage facilities are critical for preserving harvested crops. While much attention is often given to temperature control, ventilation, and pest management, lighting is another key factor that directly impacts the safety, efficiency, and compliance of a grain store.
In this blog, we’ll explore the key requirements and best practices for lighting grain storage facilities, including regulatory standards, safety considerations, and energy-efficient options.
Why Lighting Matters in Grain Stores
Proper lighting in grain stores is essential for:
- Worker safety: Adequate illumination helps prevent accidents in dusty, uneven, or confined areas.
- Operational efficiency: Good lighting allows for clear visibility during inspection, maintenance, and handling of grains.
- Pest control: Visibility supports early detection of pests or spoilage.
- Regulatory compliance: Failing to meet lighting standards can lead to penalties or business interruptions.
Key Lighting Requirements
1. Minimum Illumination Levels
Lighting levels are typically measured in lux (lumens per square meter). While specific requirements vary by region and authority, a general guideline for recommended lux levels is:
- General storage areas: 100–200 lux.
- Inspection and work areas: 300–500 lux.
- Emergency exits and access ways: Minimum of 50 lux, with emergency lighting installed where required.
These levels ensure visibility without glare or excessive brightness that could cause eye strain.
2. Lighting Design and Layout
Good lighting design includes:
- Uniformity: Avoiding dark spots and shadows.
- Fixture placement: Ceiling or wall-mounted fixtures positioned to reduce glare and maximize coverage.
- Height and spacing: Adapted to the building’s architecture to ensure full visibility.
3. Dust-Proof and Hazard-Rated Fixtures
Grain dust can be combustible and pose an explosion risk. Lighting fixtures in these environments must often comply with:
- ATEX (Zone 2) or IECEx standards (in Europe and internationally).
- Class II, Division 1 or 2 rating (in the U.S.).
Where required, use explosion-proof or dust-ignition-proof fixtures to mitigate fire hazards and ensure regulatory compliance.
4. Emergency and Exit Lighting
In the event of power failure or emergency evacuation, reliable emergency lighting is critical. Grain stores must be equipped with:
- Battery-backed emergency lights.
- Clearly marked and illuminated exit signs.
- Escape route lighting that remains operational for at least 180 minutes during outages.
Energy Efficiency Considerations
Lighting can account for a significant portion of a grain store’s energy use. Upgrading to LED lighting offers:
- Longer life spans (50,000+ hours).
- Lower heat emission.
- Instant-on functionality (important in cold or dark conditions).
- Reduced maintenance needs.
Pairing LED systems with motion sensors or daylight harvesting controls can further reduce energy use.
Maintenance and Inspection
Regular inspection and maintenance are necessary to ensure lighting remains effective. Consider:
- Cleaning fixtures to remove dust buildup.
- Replacing damaged or flickering lights immediately.
- Documenting inspections as part of your health and safety program.
Conclusion
Lighting is more than a convenience in grain storage - it’s a cornerstone of safety, efficiency, and compliance. By following lighting requirements and best practices, you can improve working conditions, preserve grain quality, and avoid potential hazards.
Whether you're building a new facility or upgrading an existing one, consult with qualified lighting and safety professionals to ensure your grain store lighting meets all relevant standards.