Why are ATEX Lights Required for Inspection Pits?
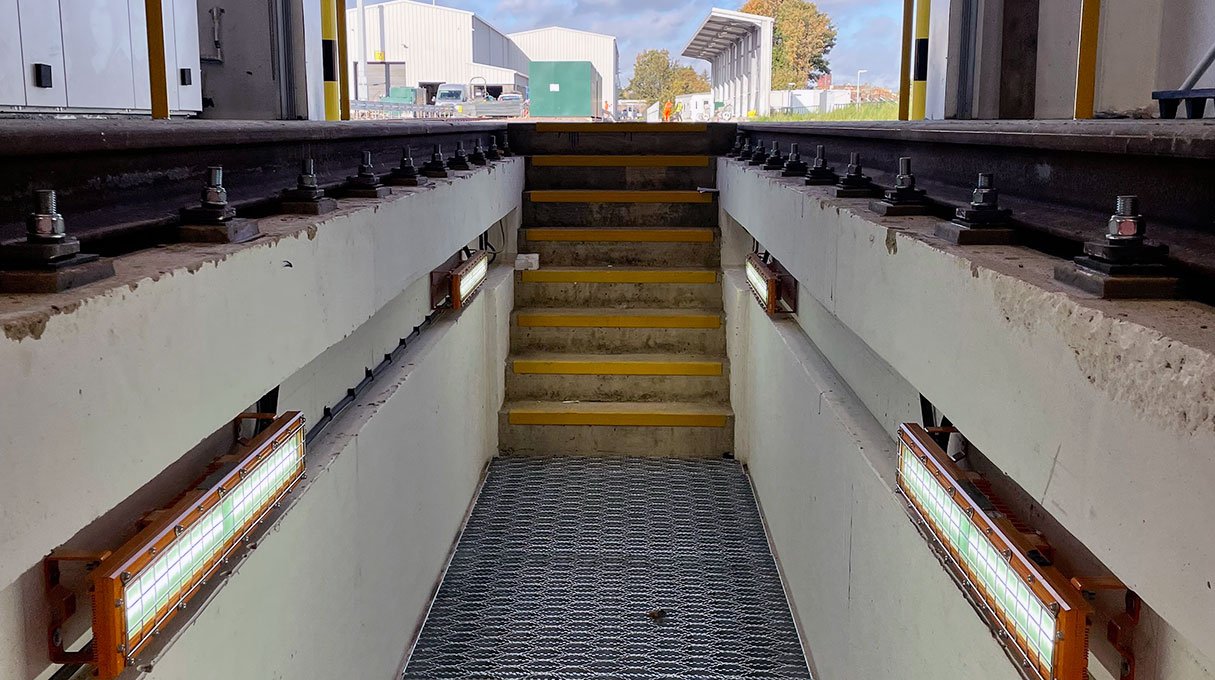
ATEX lights are often required for inspection pits because these areas are can be classified as hazardous environments where explosive atmospheres can form, typically due to the presence of flammable gases, vapours, or liquids, such as fuel or oil. Here’s a breakdown of the reasons/characteristics where Inspection Pit ATEX Lighting would be required:
Risk of Explosive Atmospheres
Inspection pits—especially in facilities like vehicle workshops, garages, or fuel depots—can accumulate flammable vapours. Since these vapours are heavier than air, they settle in low-lying areas like pits, creating an explosion risk.
Legal Compliance (ATEX Directive)
In the EU, the ATEX Directive (2014/34/EU) mandates that all electrical and mechanical equipment used in potentially explosive atmospheres must be ATEX-certified. This ensures the equipment is:
- Spark-free
- Appropriately sealed
- Designed to operate safely in hazardous zones (Zone 0, 1, or 2)
Prevention of Ignition Sources
Regular lighting can produce sparks, high surface temperatures, or arcs, all of which can ignite flammable atmospheres. ATEX-certified lighting eliminates these ignition sources by:
- Encasing components in explosion-proof housings
- Using intrinsically safe circuits
Maintenance & Inspection Safety
When workers are in the pit conducting inspections or repairs, proper lighting is essential. ATEX lights provide this illumination safely, minimizing the chance of an accident due to explosion.
Identifying the Zone Classification of an Inspection Pit
Determining the ATEX zone classification for an inspection pit involves assessing the likelihood and duration of the presence of explosive atmospheres (usually flammable gases or vapours). This process is typically part of a hazardous area classification (HAC) assessment, often done by safety engineers or risk assessors. Here's a breakdown to guide you:
ATEX Zone Classification for Gases/Vapours
Zone | Definition | Example in Inspection Pits |
Zone 0 | Explosive atmosphere is present continuously or for long periods | Rare in pits, but possible if there's a constant fuel leak |
Zone 1 | Explosive atmosphere is likely to occur during normal operation | Fuel vapours may enter the pit frequently during vehicle maintenance |
Zone 2 | Explosive atmosphere is not likely in normal operation, or only for short periods | Fuel vapours might occasionally reach the pit if there's a spill or tank venting nearby |
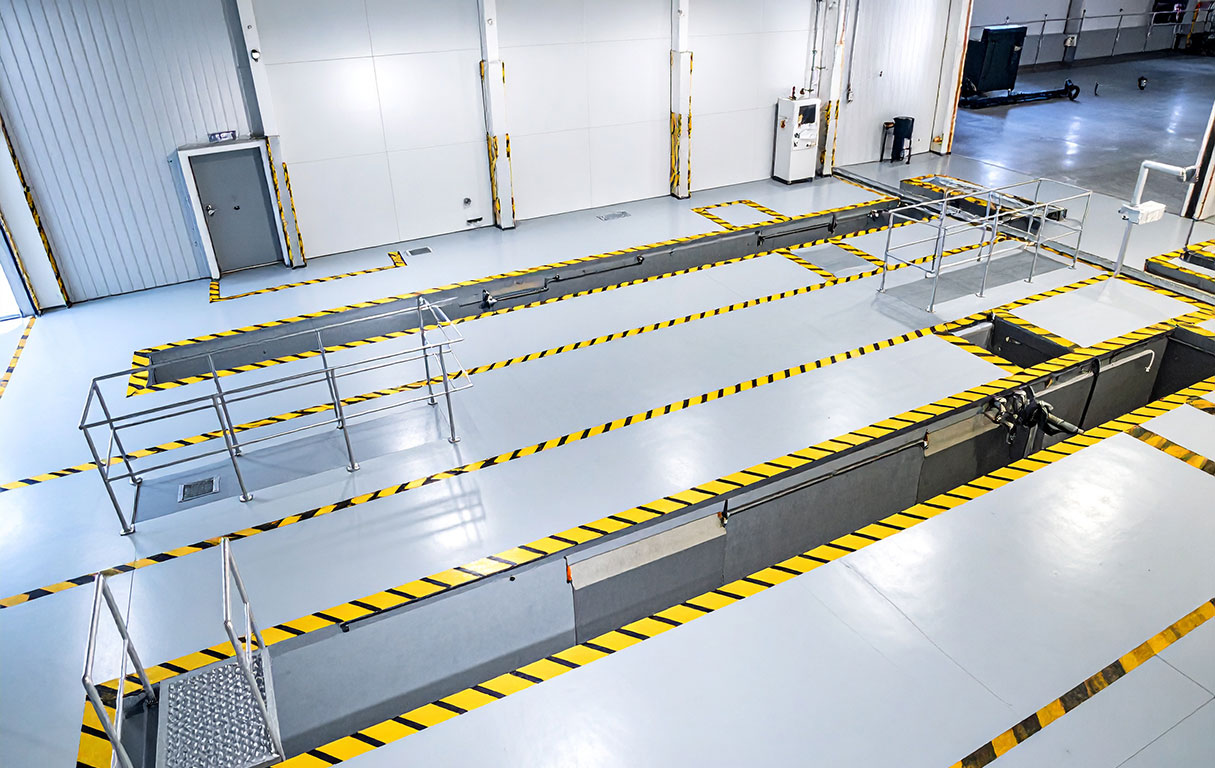
Steps to Determine Your Pit’s ATEX Zone
1. Identify Hazardous Substances
- What fuels, solvents, or chemicals are used nearby?
- Are LPG, petrol, diesel, or brake cleaners involved?
2. Assess Ventilation
- Is the pit naturally or mechanically ventilated?
- Poor ventilation = higher ATEX zone
3. Evaluate Frequency and Duration of Exposure
- How often are vehicles over the pit?
- Are engines running or being refuelled nearby?
4. Consider Spill and Leak Risks
- Does fuel regularly spill into or around the pit?
- Are there drain points or vapor traps in the pit?
Example Classifications
- Zone 1: In a garage where vehicles with fuel tanks are regularly serviced, and ventilation is poor, the pit might be Zone 1.
- Zone 2: In a well-ventilated garage with only occasional fuel exposure, the pit might be Zone 2.
- Unzoned (safe): In electric vehicle-only workshops or pits with zero exposure to flammable substances, it might not need zoning (but this is rare).
What You Need to Do
- Conduct a Risk Assessment: Required under the ATEX Directive and DSEAR (UK).
- Document the Zone Classification: Create a hazardous area drawing.
- Select ATEX-Certified Equipment: Ensure lights, tools, and any electrical components meet the correct ATEX zone and gas group requirements.